In ceramic roller kilns, the behavior of the material during its advancement can vary between the center and the sides. These differences have a direct impact on the quality of the final product and require specific technical adjustments to optimize the process. The main considerations related to these variations are detailed below.
Cooking zone
In the firing zone, the material moves faster on the sides and slower in the center. This behavior is related to the softening of the material due to heat and its own weight, which affects its capacity for uniform movement.
If the plane of the rollers does not present a more rectilinear advance, one roller marked with its taper can be placed in an orderly and alternating manner at the handling end and another marked at the bearing support end, also in blocks of 5 or 10 equal rolls at the handling end and another 5 or 10 equal at the supporting end, perhaps with 40 / 50 rolls until the exit from the cooking area
In addition, it is always advisable to alternate between a drive roller and a support roller to ensure a better distribution of the feed.
Depending on the degree of deceleration in the centre of the kiln rollers, this formula may also have to be used from the preheating zone until the start of the cooking zone, which is approximately 10 metres long and temperatures ranging between 700 and 900ºC

Rapid cooling zone
In the cooling zone, the behavior of the material changes, advancing more rapidly through the center than through the sides. For this purpose, rollers of Pyroxal “ZR” quality, developed specifically by ICRA for this zone of the furnace, are used.
Mixing rollers (SILICON CARBIDE + CORDIERITE) have been created for this area, which prevent the deformation of the rollers and the material between the last cooking zone (+1,180oC) and the first quick-cooling zone , produced by the blow-off tubes at +610oC; since silicon carbide has a higher THERMAL CONDUCTIVITY and a low coefficient of expansion, it is better able to withstand such temperature differences.
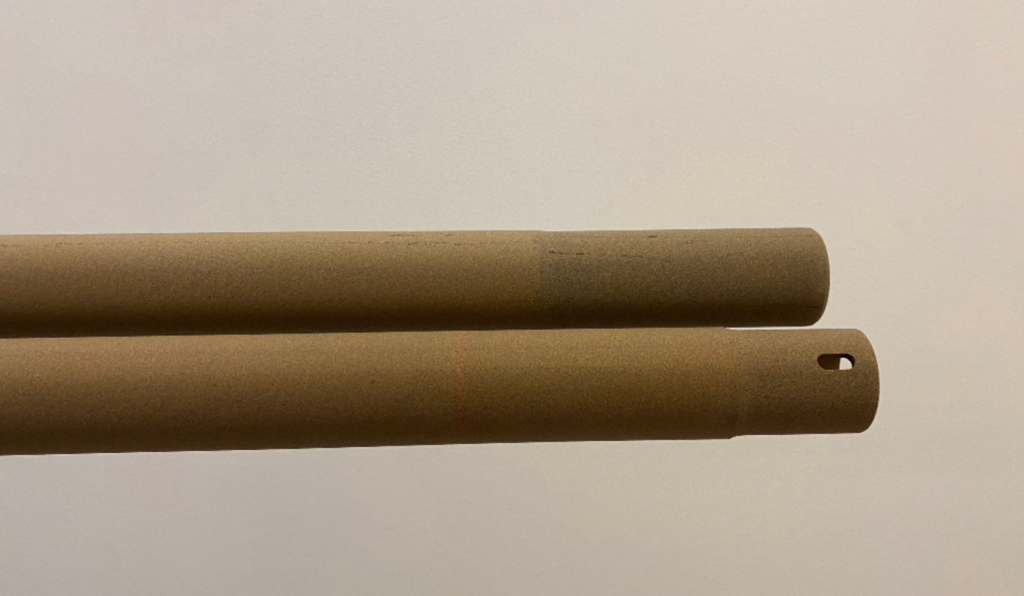
General data on heat treatment
The heat treatment of the material in the ceramic kiln goes through different critical phases, each with specific effects on the material properties:
- From 0 to 100 °C: elimination of the humidity of the piece.
- From 200 to 400 °C: combustion of organic materials, such as glycols, fixatives and glue granules.
- At 572 °C: transformation of quartz from alpha to beta phase, with an increase in volume due to dimensional change.
- Fluxes (sodium, potassium and calcium) reduce the melting temperature of other raw materials.
Important information on rollers
When the various contaminants are incorporated into the roller matrix, new crystalline phases with different expansion coefficients are generated, thus modifying the homogeneous structure of the roller.