The ceramic industry has experienced a growing demand for technologies to improve energy efficiency and reduce operating costs. In this context, energy-efficient burners have emerged as an innovative solution to optimize the combustion process in ceramic kilns.
What is the High Efficiency Burner?
It is a device designed specifically for the ceramics industry, combining advanced technology with a focus on energy efficiency and emissions reduction. This burner is characterized by its compact design and its ability to operate with a wide range of fuels, including natural gas, liquefied petroleum gas (LPG) and diesel.
Features and benefits
Compact flame: the gas nozzle and the air diffuser work together at micrometer distances, resulting in a compact and uniform flame.
Mixed combustion: the burner uses a centrifugal and radial mixed combustion approach, ensuring efficient and controlled combustion.
Adaptability to different fuels: including natural gas, liquefied petroleum gas (LPG), liquefied natural gas (LNG), among others.
Increased flame temperature homogeneity: the burner design allows a more homogeneous flame temperature distribution, even in large kilns, which reduces the problems of shade and caliber changes in ceramic products.
Reduced heat dissipation: part of the mixing air escapes through the jacket slots, preheating while keeping the nozzle at a low operating temperature, which reduces heat dissipation to the kiln wall and improves the efficiency of the firing process.
Energy-efficient operation
The blue flame indicates complete and efficient combustion, which maximizes energy efficiency and reduces the formation of unwanted by-products.
Optimal air/gas mixture: it is designed to achieve an optimal air/gas mixture, ensuring uniform and controlled combustion.
Operational flexibility: offers a wide operating range in the air/gas ratio, providing flexibility in adjusting the process according to specific production needs.
Reduced energy consumption: by making it possible to work with less combustion air while maintaining the same combustion atmosphere, it contributes to a significant reduction in energy consumption compared to conventional burners.
In addition to improving energy efficiency, it also promotes greater consistency in the quality of the final product by minimizing changes in the combustion atmosphere. This results in a reduction of defects in ceramic products and greater uniformity in final properties.
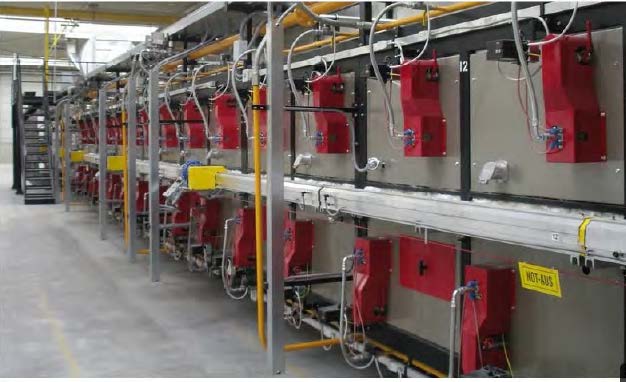